Creating Custom Finishes
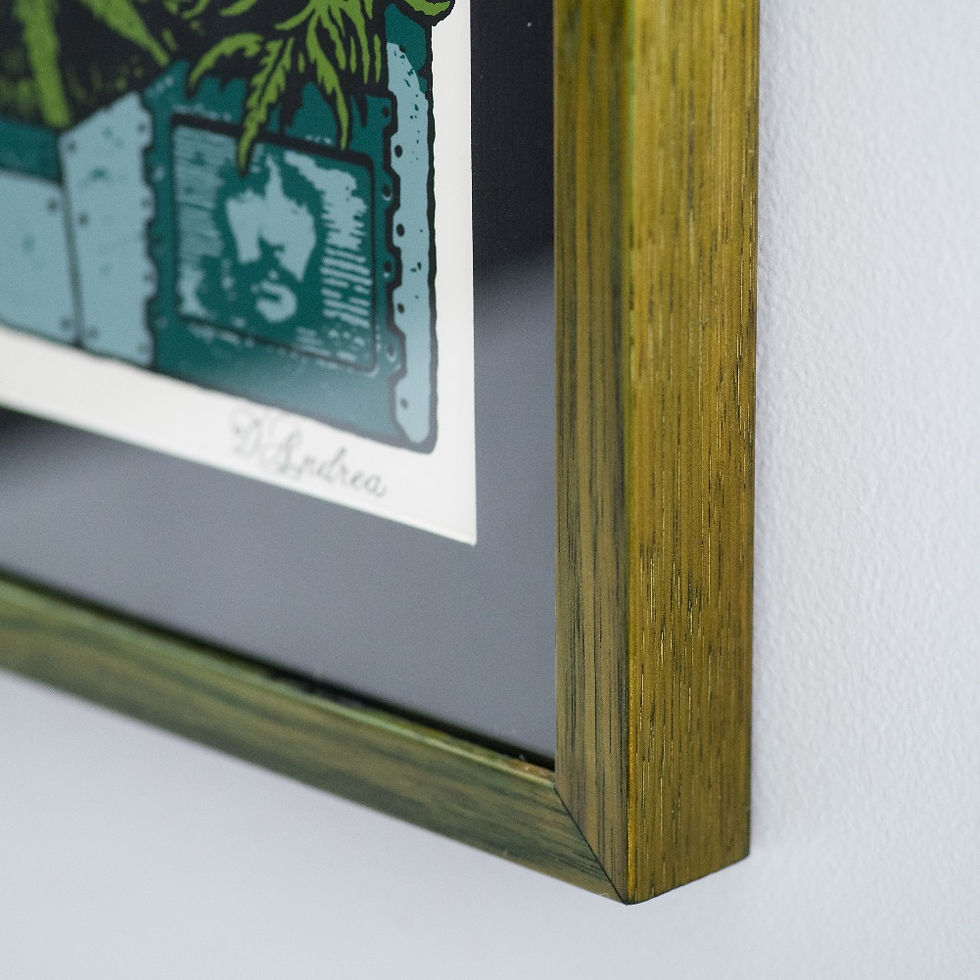
I have written before about conservation framing, the materials used and the standards to be upheld. Now I’d like to talk a little more about some of the products and techniques I use to create my own unique custom finishes.
Although I can offer the same off-the-shelf mouldings that other framers stock, most of the frames I make are constructed from raw Tasmanian Oak, finished with non-toxic, food and child-safe dyes, oils and waxes. This is in part simply because it is how I prefer to work – it’s a skill I enjoy exercising – but it also allows me to tailor the frame to the artwork it is to house. Like most framers, I have an array of corner samples on display to help clients compare various combinations of mouldings and matts, but often unique works of art require a more personalised approach, particularly if the client is looking for something a little bolder than the average wood tone. One of the reasons I prefer to use U-Beaut’s water-based dyes is that they come in a range of simple but bold colours, ideal for mixing and creating my own tones. Even better, these dyes are completely non-toxic and food safe which makes them much more pleasant to use than commercial stains, which are invariably highly toxic and give off nasty fumes.

To deepen the colour and offer an initial layer of protection, I usually add a coat of Organoil’s Danish Oil. It has a pleasant citrus scent and, although it is classified as a potential skin irritant in its liquid state, it is non-toxic and food safe once it has dried. To top things off, I apply one or two coats of U-Beaut’s Traditional Wax. This is another non-toxic and food safe product which protects the timber and can be buffed with a soft rag to create a nice sheen.
Another reason I prefer to work this way is that any damage to the finish on the frame can be easily fixed. Off-the-shelf mouldings, usually made from some sort of engineered wood with a thin outer coating of “finish”, chip easily and cannot be touched up. My frames, by contrast, are more durable and can be sanded back to the original wood and re-finished entirely if required and any loss of sheen over time can be rejuvenated with a light coating of wax and a quick buff.
Other finishing products I regularly use include India ink, shellac and even black tea. I also offer a selection of specialised finishes including liming, French polishing (with either shellac or beeswax), a Danish soap finish (characteristic of modern Danish furniture) and ebonizing, a non-toxic chemical process which blackens timber without the use of dyes or pigments. I'll talk about some of these finishes in future posts.
